Pengamanan Wisuda Telkom University, Lima Personel Polsek Dayeuhkolot Gabung Apel di Pos Gatur Kersen Bojongsoang
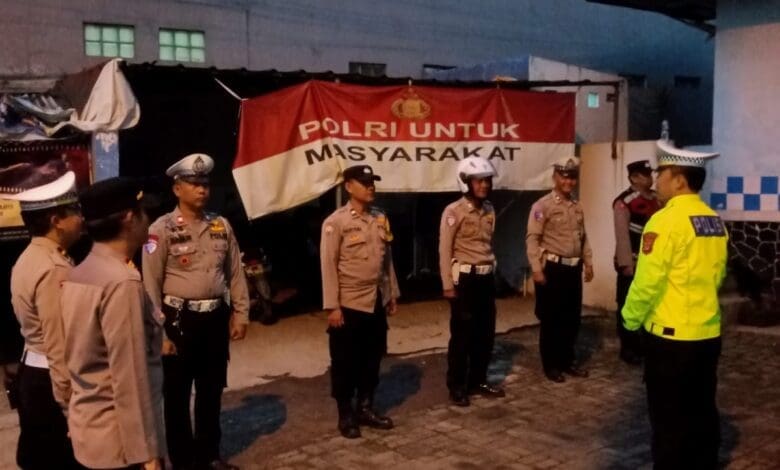
Dayeuhkolot – Dalam rangka pengamanan kegiatan wisuda mahasiswa dan mahasiswi Telkom University, lima personel Polsek Dayeuhkolot mengikuti apel gabungan bersama Polsek Bojongsoang dan Polresta Bandung. Apel dilaksanakan di Pos Gatur Lantas Kersen, Bojongsoang, pada Sabtu (10/5/2025).
Apel gabungan ini bertujuan untuk memperkuat koordinasi dan kesiapan personel dalam mengantisipasi potensi gangguan lalu lintas serta menjaga keamanan dan ketertiban selama prosesi wisuda berlangsung.
Kapolresta Bandung Kombes Pol Aldi Subartono, Melalui Kapolsek Dayeuhkolot AKP Triyono Raharja, di tempat terpisah menyampaikan bahwa pengamanan dilakukan secara terpadu untuk memastikan kelancaran kegiatan.
“Pengamanan ini kami lakukan sebagai bentuk pelayanan kepada masyarakat, khususnya kepada civitas akademika Telkom University dan keluarga wisudawan, agar kegiatan berjalan aman dan lancar,” ujar Kapolsek Dayeuhkolot.
Selain pengamanan, personel juga disiagakan di titik-titik rawan kepadatan untuk mengatur arus lalu lintas dan membantu pengguna jalan.
Kapolsek berharap masyarakat dapat mendukung kelancaran acara dengan mematuhi arahan petugas di lapangan.
Acara wisuda Telkom University dijadwalkan berlangsung sepanjang hari dengan dihadiri ribuan tamu undangan, sehingga rekayasa lalu lintas juga disiapkan untuk meminimalisasi kemacetan di sekitar kawasan kampus dan jalur utama Bojongsoang.***
Darmanto (Red)
Source link